- Home
- Blogs
05.05.2021
Core Kiteboarding XR7 launch and interview: Frank Ilfrich Core Kite designer
Check out the new Core XR7 here
The time has finally come again: Core Kiteboarding is launching a new kite model - the XR7 Kite! For the launch of the XR7 we have something special for you: We do not only stock the XR7 already, but we offer you a look behind the scenes: We met Frank Ilfrich, Head of R&D at Core Kiteboarding and Carved, for an interview and learned a lot about kite development at Core Kiteboarding, got some insights about the development of the new XR7, what challenges there were and what Frank, as the leading designer, is the proudest of. As Core maintains a super high manufacturing quality since years, we also touch base on that! Check it all out in this interesting interview below – have fun!
To get you extra excited for the following interview, check out this badass product video of the new XR7 first!
Interview with Frank Ilfrich, Head of R&D, Core Kiteboarding & Carved
Frank… please give us a quick introduction on who you are and what you do!Hi, I'm Frank Ilfrich. I am a kite designer and Head of R&D at CORE. I have been kiting for over 20 years and have been working for CORE and CARVED since 2005. I enjoy kiting - whether on a twintip, directional or foil. Since good waves are very rare on Fehmarn though, the directional is mostly coming out on vacation or on test trips.
Can you give us a run through of development of Core products – especially Kites?
Every product goes through three development phases: first, we analyse what the product must be able to do, for which target group it should be suitable, etc. Second, we get into the design phase and finally into the testing phase. However, the development process differs a bit depending if you are designing a new model or continue an existing series.
For example, for the first model of the XLite we used the Nexus as a basis. The Nexus had already proven itself and it worked very well in many aspects. From there we started and made as much changes as we needed to until we met all the requirements, we set for first version of the XLite - in other words, it does exactly what it should and is also easy to use and stands out from other kites. With kites like the XR, which we have in our product range since years, the analysis phase begins by evaluating the feedback we have received from our dealers, importers and schools, team riders and end customers we have received. We value this feedback a lot. In addition, as a developer, of course you already have ideas in mind that you want to tackle and try to realize. Another factor to be taken into account are new materials. These make innovations possible in the first place and, conversely, also require adjustments. The requirements for the next kite model are being defined by these factors. After all our analysis we move into the design phase.
In the design phase, these requirements then have to be implemented in our products. Thanks to years of experience, we know which twists we have to do in order to meet the requirements we defined earlier. We design different models, e.g. A, B and C in our design software, send them to the factory and 10-12 days later we have our prototypes here on Fehmarn for testing.
In the test phase, the prototypes A, B and C will compete against the current model and will be evaluated for specific details but also overall performance. I then collect feedback from team riders as well as normal kiters. Testing products is really a strenuous and time-consuming process. Testing properly is something you have to learn. In addition to the experienced testers, I always let people fly the prototypes who simply use the products as they normally would do and collect their unfiltered feedback. As soon as we are satisfied with the final prototype, the kite goes into production.
Even if the kite already exceeds our expectations, for me as a designer you sometimes still have the need to touch certain details again or think you could rework the trim once more, etc. Often you have a gut feeling that this could have an interesting outcome, but at some point you have to come to an end as well. I then put all the ideas that I could not fully test out into the first prototypes of the next generation. The development then continues seamlessly.
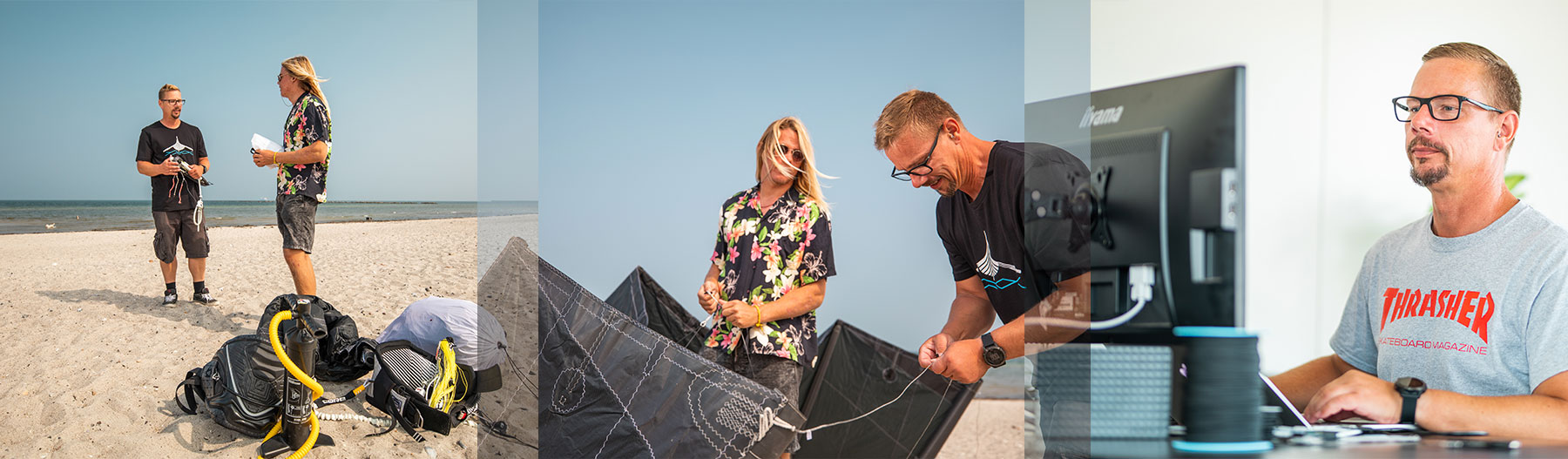
Are you, and if so, how are you gathering data using technical devices in testing to include them into your analysis?
In our tests, we use simple devices such as the WOO and GPS trackers to compare jumping heights or upwind properties. Back then we have started a project with the University of Berlin to evaluate methods to measure line pressure etc. and we still do simulate and measure aerodynamic flow in our kites. However, it has to be said very clearly that all these devices and simulations cannot capture the fun of a session on the water and that is ultimately what it is about. On paper, the performance data of a prototype might seem a little better, but the interaction of all the factors is so complex that it simply cannot be simulated - no computer system in the world has yet been able to do that. Therefore, humans remain the best measuring instrument for us.
The XR is looking back on proud 12 years of development and thus on hundreds of prototypes. I guess the biggest development steps nowadays are to be achieved using new materials. What is happening there?
In terms of materials, a lot has happened on the market in general in the last two years. We are now using the new CoreTex 2 cloth for the first time with the XR7. It took a total of roughly three years to develop this new cloth. With the CoreTex 2 we deliberately concentrated on the coating of the cloth, as there are some serious differences in this area with regards to durability, elongation, tear resistance, etc. However, for me as a designer or as a manufacturer in general, a new material always comes with a certain risk of course. In the field of new materials we also want to break new ground and we do have more in our quiver than we reveal, but we always have to proceed very carefully and of course test everything new in detail.
The XR has a very broad fan base - from big air pilots jumping + 30m to kite students who just learned how to ride. Is it more difficult or more complex to work on a kite with such a wide fan base compared to kites like the XLite or Section from the Specialized Series?
With our products from the Specialized Series it is actually a bit different at the kite is tailored exactly to one use – whether it’s the XLite for foiling or the Section for waves. The challenge here is that those products need to be absolute top performers and nevertheless, these products must also remain manageable by everyone - except for the Impact maybe ;-)
With kites from the Universal+ Series such as the XR, there is often a wider range of requirements, as the kites must be suitable for several disciplines and kiters. In addition, this performance must be easily accessible as well. As a designer, of course, you always want to develop the product further and add more performance to it, also because you develop yourself further, just like the customers. However, there are always people who are new to the sport. Therefore, as a designer, you may not always be able to implement everything you wanted. On the other hand, it is also a great challenge to equip the kite with more power, but still keep it easy to use and maintain its character. For example, with the XR we already had prototypes that were able to achieve a higher maximum jump height. However, this performance was only accessible to very advanced riders. We then decided to go with the prototype as our final model, that was easier to jump. As a designer, I always keep our customers in mind and see their perspective: You simply have more fun on the water with a kite that jumps easier. So, you always have to consider which direction you want to pursue, but so far we have always managed to find the right balance very well.
What was the initial vision for the new XR7 and how did you work towards it?
The clear goal of the XR7 was not only to increase the performance, but also to increase the turning speed and steering precision. The XR customer grows with the kite and formats like the KOTA and riders like Janek Grzegorzewski keep pushing the limit that is now expected from kites like the XR. Specifically, it was clearly a goal to implement the improved CoreTex 2 cloth in the XR7, as it enables more performance and more stability.
New materials always mean adjustments to the kite design. If a parameter like the cloth is changed, you must do various adjustments to adapt the kite design to the new material. In case of CoreTex 2, for example, we gain performance and flight stability through a new coating, but the associated lower stretch in the flight cloth also means less twisting of the kite when steering. LE and strut diameter, bridle setup, etc. are options to influence this and of course the desired lower total weight.
As the leading kite in the worldwide Woo ranking, we naturally want to continue to play at the top with the XR and further improve its top performance. We are always trying to push this forward without having to accept any compromises in terms of ease of use.
What innovations can we look forward to with the XR7 and what effects do these innovations have for ambitious riders and beginners? What aspect are you particularly proud of as a developer?
The new, more powerful CoreTex 2 and the reduced weight of the XR7 are probably the most noticeable innovations. More power, still more playful for freeriding and in waves but also positive effects for big air and Kiteloops.
Of course I'm happy that we currently hold the WOO high jump record, but I'm just as happy about satisfied cruisers and freeriders who have a good time on the water, or even beginners who are learning to kite with the XR. I don't think there are many kites that can serve such a broad target group.
What challenges did you face in developing the XR7 and how did you overcome them?
The mix of new materials and the requirement to always do everything better without compromising on other aspects is the central challenge. Or to put it simply, to develop an exciting kite that feels fresh but still familiar.
Was the development of the XR7 affected by Corona and if so, how?
Of course, the situation didn't really make things easier. Fortunately, we were able to continue testing in Germany in spring and most of our suppliers were able to continue working, but it made a lot more difficult and cost time and nerves. We were happy, when we were able to test the XR7 in Cape Town with great success.
With the Sensor 3 Bar that was introduced last year, we faced significantly more stumbling blocks due to Corona, such as material availability, delivery delays, etc.
Core kites have been celebrated - among other things – for their high manufacturing quality. Can you tell me more about the production and how this is achieved? We are very happy and proud that we have been working together successfully with our production facility in Sri Lanka for so long. In 2005 we built up production there from scratch and really did a lot of pioneering work in production. In the beginning, the entire production was quite simple, but soon they reached a very high level of professionalization there. The entire production is ISO-certified, every step in the process is being recorded using bar codes and through years of cooperation and experience, an enormous amount of knowledge has been built up there in production. If I propose design ideas to them, they can address them directly and give me feedback on it.
I am still on site very regularly and check out the entire production process and see where, for example, new work steps are created or how new processing methods or machines are being applied. Therefrom, I also get impressions that I can incorporate into my work.
All in all, we are super lucky to be seen as part of the family and this attitude and the attention to detail ensures high quality and reliability. In production, both sides do their best to continuously improve this high level of quality. Apart from that, there is a really a great working atmosphere in production, the employees feel at home there, people laugh and listen to music and the employees like to work there - I've known some of the workers there now for 15 years and they have been promoted from being a sewer to department heads over the years etc. - all of this is also ultimately related to our products and quality.
Many brands in the kite industry face stock shortages currently... What is the availability of the new XR7? Can anyone who wants to fly the new XR7 order the kite directly or do customers have to be prepared for waiting times?
We are in the fortunate position of having a good inventory of materials for kite production due to our purchasing strategy and our design philosophy. Of course, fewer cloth colors also help in this situation ;)
Let's assume the new XR7 is out and the team riders have adapted to the new kite and there is a huge storm coming up in the forecast ... which heights can be reached with the XR7? Will there be a new height record soon?
The height rankings have gained a special dynamic in recent years and team riders from all brands are motivated and battle each other with their teammates and friends. But many do it for fun, it's more about the adrenaline rush and the results are a side effect. I know that the girls and boys do not prepare specifically for this, but simply step on the gas when it fits.
I think there is still quite a lot of hidden potential regarding jump heights, especially in terms of materials, but of course the rider's shape on that day is still the major factor. The days on which +30m jumps are possible are not that frequent either - so many factors have to come together for that, but I am also very curious what we are going to see!
Awesome – thank you very much for your time and sharing these insights with us!
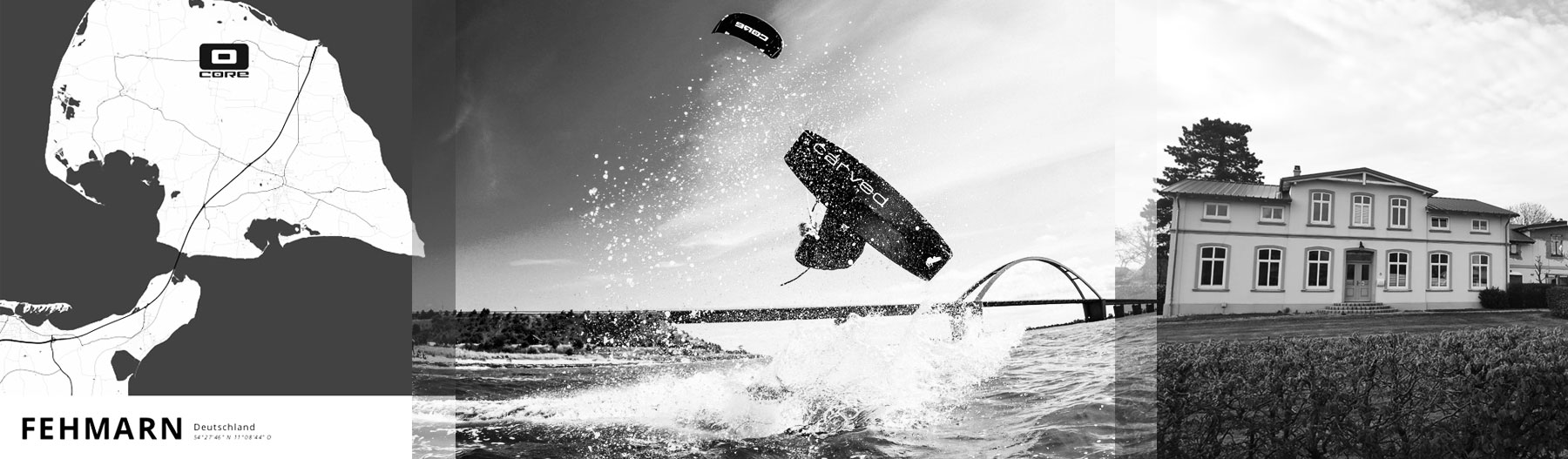
Added to basket
Subtotal | € 0,00 |
Shipping costs NL | € 0,00 |
Total (incl 0% VAT) | € 0,00 |
You have no product(s) in you basket.
Weet je niet waar je moet beginner?
Contact our customer service for advice